Discover how FineVinyl is manufactured to deliver unmatched clarity, consistency, and dimensional stability. Go behind the scenes of Extruflex’s precision calendaring process and see why engineers and OEMs trust FineVinyl for high-performance PVC applications.
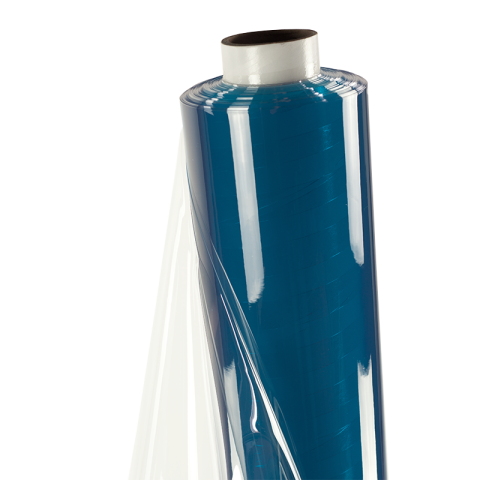
Great performance starts with a great process.
At Extruflex, we believe that the quality of a PVC film is determined long before it’s unrolled on your shop floor. That’s why our FineVinyl range is built on a foundation of advanced calendaring, rigorous material selection, and tightly controlled production parameters.
FineVinyl isn’t just known for its clarity and dimensional stability — it’s trusted because of how consistently it delivers. Whether used in high-frequency welding, tent fabrication, soft glazing, or industrial covers, each roll represents decades of technical refinement.
In this post, we invite you inside our manufacturing process to explore what makes FineVinyl a standout solution for professionals who demand precision, repeatability, and performance.
How FineVinyl is made: A closer look at the manufacturing process
FineVinyl’s performance is no accident — it’s the result of a carefully engineered production journey. From raw material formulation to the final winding of each roll, every detail is optimized to deliver technical consistency and reliable quality. Here’s how that process unfolds, step by step.
1. The calendaring and lamination process – A quick overview
At the heart of FineVinyl’s consistency and surface quality lies the calendaring and lamination process — a precision technique essential to producing high-performance flexible PVC films.
Calendaring is distinct from extrusion in both method and outcome. In this process, a pre-compounded PVC formulation is first thermally conditioned and plasticized to achieve a uniform melt. This homogenous material is then passed through a series of polished, temperature-controlled rollers known as a calendar stack.
Each roller serves a purpose — whether controlling thickness, adjusting surface finish, or ensuring sheet stability. By applying carefully modulated pressure and heat, the film is compressed and flattened to exacting tolerances, resulting in a sheet with highly consistent gauge, superior transparency, and a flawless double-polished surface.
The lamination allows stacking multiple layers of clear films to make at the end a super clear double polished film with the highest possible clarity.
Unlike extrusion, where flow dynamics can introduce variability in thickness and finish, calendaring delivers:
- Exceptional dimensional control across the entire roll width
- High optical clarity free from flow lines or die marks
- Tight thickness tolerances critical for downstream fabrication
For applications where visual quality and repeatability are non-negotiable — such as tent windows, printed overlays, or flexible partitions — calendaring plus lamination is the gold standard. It is not just a method of production; it is a commitment to consistency, engineered into every meter of FineVinyl double polished clear vinyl.
2. Precision matters – Quality that’s built into every roll
Consistency isn’t a byproduct of the FineVinyl process — it’s a foundational principle. From the moment raw materials are introduced to the system through to the final winding of each roll, FineVinyl is governed by a tightly controlled quality framework designed to meet demanding industrial and OEM standards.
It begins with precise formulation control. PVC resins, plasticizers, stabilizers, and performance additives are weighed and blended to exact ratios, ensuring homogeneity before the calendaring phase. This step is crucial: a consistent compound leads to a consistent film.
Throughout production, we maintain tight manufacturing tolerances — not only on thickness but also on roll width, surface flatness, and optical clarity. These tolerances are continuously monitored via inline inspection systems, which provide real-time feedback on key parameters such as film gauge, surface defects, and visual uniformity.
Beyond the line, we conduct routine laboratory testing on each production batch to validate:
- Shore A hardness to confirm material flexibility
- Colour consistency across visual and instrumental spectrums
- Tensile and tear strength for mechanical reliability
- Aging and UV resistance
- Cold Temperature resistance
This multi-layered approach to quality control results in a film that performs predictably — regardless of batch or delivery. For customers, that means fewer surprises during cutting, sealing, printing, or lamination; reduced waste; and higher throughput in downstream applications.
With FineVinyl, quality isn’t assumed — it’s measured, verified, and delivered in every roll.
3. Material options to match your application
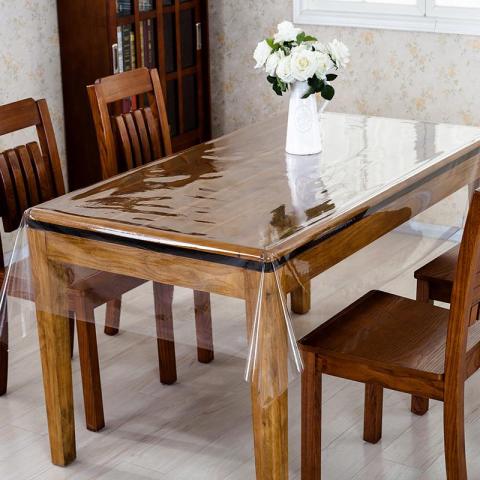
FineVinyl is more than a single product — it’s a versatile platform built to serve a wide spectrum of technical applications. Whether you're developing transparent architectural elements, marine enclosures, or industrial curtains, the material behind your project must meet performance targets with precision. That’s where FineVinyl excels.
At the core of this adaptability is hardness tuning. FineVinyl can be custom-calendared to meet specific flexibility or rigidity requirements using the Shore A or S-scale rating system. For example, softer grades (e.g., 3S) offer enhanced pliability for complex sewing or welding, while stiffer grades (e.g., 2S) provide better structure and resistance in tensioned applications like window panels or coverings.
We also offer a curated selection of special formulations tailored to distinct operational environments:
- Standard Double-Polished Clear – For unmatched transparency and visual clarity.
- Low Temperature – Maintains flexibility and impact resistance when temperatures drop to freezing levels.
- Anti-static – Ideal for static-sensitive environments such as electronics packaging, data centers or cleanrooms.
- Marine grade – With enhanced UV resistance and durability for continuous outdoor and nautical exposure.
- Fire Retardant (BS7837 / M2 / B1 Grade) – Specifically developed for markets requiring flame-retardant performance, particularly in the UK and EU.
Each variant is produced under the same tight tolerances and quality control protocols, ensuring consistency regardless of grade or finish.
Whether you're selecting film for optical performance, mechanical behavior, or environmental resistance, FineVinyl provides a stable, customizable foundation that supports your engineering and fabrication goals.
4. Flatness, handling, and dimensional stability
In high-spec applications, how a film performs during handling and fabrication is just as important as its chemical or optical properties. That’s why FineVinyl is engineered not only for clarity and strength — but also for real-world usability.
One of its most defining characteristics is its exceptional flatness. FineVinyl is manufactured with calibrated tension and cooling cycles that eliminate surface waviness, edge curl, or roll memory. This ensures the film lays perfectly flat when unrolled — a critical factor for operations like:
- Digital or screen printing
- High-frequency welding or RF sealing
- Stitching and sewing into multi-layered assemblies
- Bonding to rigid or flexible substrates
Ease of handling is also a major advantage. Each roll is uniformly wound with consistent edge alignment and low telescoping, making it easier to load onto machines, unwind on tables, or process in automated systems. This reduces setup time, minimizes film deformation, and improves yield during fabrication.
FineVinyl offers excellent dimensional stability under thermal or mechanical stress. Whether exposed to cutting, heat sealing, UV light, or fluctuating ambient temperatures, the film maintains its form with minimal shrinkage or distortion — preserving both the function and appearance of the final product.
From the first pull to the final fit, FineVinyl double polished delivers a predictable handling experience that professionals can rely on.
5. Built to perform in real-world applications
FineVinyl is engineered not just for controlled environments — but for the demands of daily use across industries where conditions are anything but predictable.
From industrial curtain and swing door manufacturers to tent, awning, and marquee fabricators, FineVinyl is trusted for its long-term reliability. Its ability to maintain optical clarity, surface integrity, and mechanical flexibility under varied environmental conditions makes it a go-to choice in both interior and exterior applications.
Key performance attributes include:
- UV and weather resistance (in select formulations), ensuring visual appeal and structural integrity in outdoor installations
- Consistent flexibility over time, even after repeated bending, rolling, or exposure to temperature changes
- Colorfastness and transparency, helping maintain the film’s aesthetic and functional value for years
Whether installed in a static structure or a mobile, transportable system, FineVinyl double polished retains its performance characteristics well beyond industry norms. It’s not just built to meet specification — it’s built to last in the field.
A film you can rely on
From precision calendaring to performance-tailored formulations, every roll of FineVinyl reflects Extruflex’s commitment to quality, consistency, and real-world usability. It’s a film designed not just to meet technical specifications — but to exceed expectations in the environments where it matters most.
Whether you require high optical clarity, cold-weather flexibility, or reliable dimensional stability for fabrication, FineVinyl delivers a proven solution engineered for performance and built to last.
Ready to use FineVinyl for your next project?
Contact our team for guidance on product selection